Grinding Wheels play an important role in manufacturing and finishing processes. Thus, it provides the accuracy necessary to shape and refine materials. These tools help in cutting, grinding, and polishing various surfaces. Moreover, it also impacts the quality and efficiency of production. Thus, you must understand the difference among various wheels.
Each type of wheel has a specific use, ranging from sandy grinding to fine finishing. This variation ensures that manufacturers can select the right wheel for their requirements. Thus, it enhances performance and achieves the most reliable results in their processes. Understanding these differences will also help you to maximize efficiency and accuracy.
Materials and Applications Used in a Grinding Wheel
Generally speaking, Grinding Wheels works on various materials and applications. Here are some different materials used in these wheels along with their applications.
- Material Diversity. These wheels are made from hard materials, including ceramics, metals, and composites. These materials are great in offering unique properties for effective grinding.
- Application-Specific Needs. The wheels cater to specific tasks such as grinding for fine details and rough grinding. It further helps with material removal and cutting for shapes. Lastly, it helps in polishing for a smooth finish.
Choosing the appropriate Grinding Wheel based on materials and applications ensures optimal performance. Moreover, it also provides efficiency and the desired quality of the finished product. Now read the next section to learn about some unique types of grinding wheels.
Different Types of Grinding Wheels
Buy Grinding Wheels
Grinding Wheels come in various types that can handle specific tasks with accuracy. Here are some unique types of wheels you should know about:
- Abrasive Types. Common abrasives include aluminum oxide for general-purpose grinding. Moreover, it also includes silicon carbide for hard materials. Not only this, they also include diamonds for hard materials and CBN for high-speed steel.
- Bond Types. You can bond wheels with vitrified, resin, metal, or hybrid bonds. Furthermore, each of them offers different levels of durability and flexibility.
- Grit Sizes. They come in coarse, medium, and fine operations. Also, it handles different amounts of material removal. Thus, it helps to achieve various levels of finish quality.
You should choose the right combination of abrasive, bond, and grit. As a result, it will help you to ensure efficient grinding for various applications. In the next section, you'll learn about the performance characteristics of grinding wheels.
Performance Characteristics of Grinding Wheels
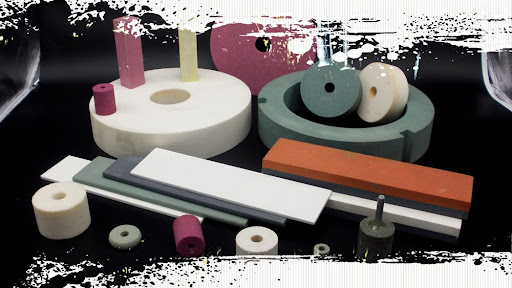
The performance conditions of Grinding Wheels are important. It helps us to achieve optimal results in various grinding operations. So, here are the performance characteristics of the wheels.
- Cutting Efficiency. Grinding Wheels enhances cutting performance based on the task. This is true for heavy material removal or accuracy work as well.
- Surface Finish. Choosing the right wheel helps achieve the desired surface finish. It includes coarse grinding as well as finish polish.
- Durability and Wear Resistance. Wheel durability impacts the longevity and efficiency of the Grinding process. Moreover, it is applicable with high-quality wheels offering wear resistance.
Understanding these characteristics ensures that the appropriate wheels are useful for each application. As a result, it improves the performance and results. Continue reading to discover the operational conditions of grinding wheels.
Operational Conditions of Grinding Wheels
These conditions affect the performance and efficiency of Grinding Wheels. So, here are some operational conditions for these wheels.
- Speed and Feed Rates. It is important to match wheels to their speed and feed rates. As a result, it helps to optimize performance and prevent damage.
- Use of Coolant. Using coolant helps to maintain wheel performance and reduces heat generation. Furthermore, it helps to achieve a better material finish. Well, you can do it by preventing overheating and improving surface quality.
You should follow these operational conditions. It will help you to ensure that the Grinding Wheels work in an effective way. Moreover, it also provides high-quality results in various Grinding tasks. In the next section, you'll get to know about the various advantages of specialized wheels.
Advantages of Specialized Grinding Wheels
Specialized Grinding Wheels offer unique advantages. As a result, they enhance the Grinding process. So, here are some core benefits of using a specialized Grinding Wheel.
- Efficiency and Productivity. The wheels can improve productivity by optimizing performance for specific materials or processes.
- Cost-Effectiveness. Using the right wheel for each job can reduce material waste and extend wheel life. As a result, it will help you to save manufacturing costs.
- Quality Control. Specialized wheels will help you to enhance quality control. Well, you can do it by ensuring consistent results and accuracy in manufacturing.
Including specialized Grinding Wheels ensures better efficiency, cost management, and consistent product quality. Up next, we will discuss some challenges you might face while using these wheels.
Challenges in Using Inappropriate Grinding Wheels
Using inappropriate wheels can lead to several challenges that impact performance and safety. So, here are the top challenges in using Grinding Wheels.
- Suboptimal Performance. Inappropriate wheels can reduce efficiency and damage the materials you are working on.
- Increased Wear and Tear. Mismatched wheels wear out faster. As a result, they may lead to higher replacement costs and frequent maintenance.
- Safety Risks. Incorrect wheels pose safety risks, including accidents and damage to equipment. Yet, it happens due to improper operation.
You should choose the right Grinding Wheels so that you don’t face these challenges. Now you must be thinking about some possible case studies about grinding wheels. Well, the next section will help you out with it. Keep reading to find out about some case studies of different abrasive wheels.
Case Studies of Different Grinding Wheels
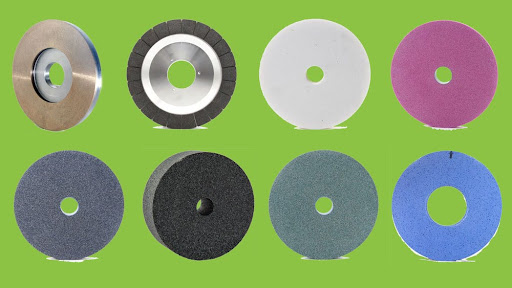
Case Studies highlight the diverse applications and effectiveness of various Grinding Wheels. So, go through this section to know some possible case studies of different wheels.
- accuracy Grinding of Hard Materials. CBN and diamond wheels are important for achieving accuracy. Moreover, it also helps to meet efficiency when working with hard materials.
- General Metalworking. People use Aluminum Oxide and Silicon Carbide wheels for general metalworking. As a result, they enhance and reduce downtime.
- High-Volume Production. Durable and efficient wheels are important in high-volume production settings. Furthermore, they can enhance productivity and reduce downtime.
These case studies show the importance of choosing the right Grinding Wheels. Thus, it will lead you to meet specific operational requirements. Furthermore, it will also help you to improve the wheel’s performance. Now, let's move on to know about the future trends of these abrasive wheels.
The Bottom Line
Choosing the right Grinding Wheels is important for optimizing performance across various applications. The appropriate wheel enhances efficiency, quality, and safety in Grinding processes. Industry experts should understand the advancements in materials and customization trends. As a result, it will help them to improve productivity and achieve superior results. Proper wheel selection ensures effective material processing. Furthermore, it also contributes to safer and cost-effective operations. So what are you waiting for? Choose the right grinding wheel and start using it now!
FAQs
Question. What are the uses of different abrasive wheels?
Answer. Abrasive wheels are available in different grit sizes. Lower grit numbers are coarser. But higher grit numbers are less coarse. Low-grit wheels are perfect for rough jobs where you don’t have to worry about the finished look of your project. Thus, you should use a high-grit wheel for a smoother finish.
Question. How can I choose a wheel?
Answer. The first thing you should consider is the object you want to use the wheel on. Moreover, you should also consider the type of material of the object and its hardness. By assessing these elements, we may examine the abrasive type. It will also help you to assess grain characteristics, grit size, and bond type.
Question. Which grinding wheel should I use for hard materials?
Answer. You should use soft grinding wheels for hard materials. Moreover, the wheel’s hardness is determined by the bond. When hard materials are processed using sift grinding wheels, the grains break and new grains are formed. This is further known as sharpening mechanisms.